An Overview of the ORR Toolkit
The ORR (safety culture assessment) toolkit was developed to allow its Inspectors to investigate key aspects of an organisation’s safety culture and to identify any concerns. It is not necessarily intended as a tool for safety culture improvement, although obviously it can assist.
The approach uses a combination of workplace inspections and observations by the Inspector and interviews with staff. Five main safety culture indicators are considered:
- Leadership
- Two-Way Communication
- Employee Involvement
- Learning Culture
- Attitude Towards Blame
These indicators are also reflected within the RSSB safety culture toolkit.
The five indicators are assessed against six scenarios and associated criteria to assist the Inspector decide whether or not the organisational arrangements in place are satisfactory – see illustration below:
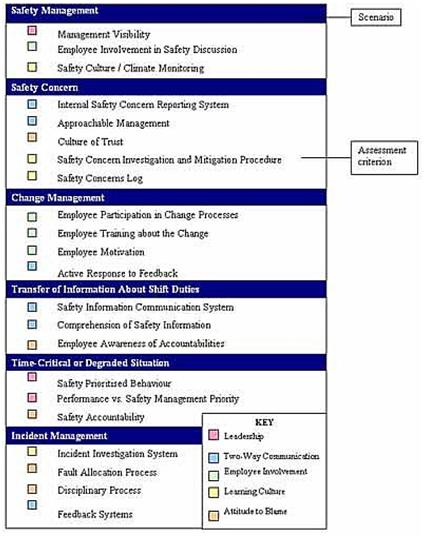
Each scenario is associated with relevant assessment criteria that include the following key expectations:
Assessment criteria | Key expectations |
Management Visibility | All management should be committed to safety and should demonstrate this by conducting regular safety tours in all operational areas. Safety tours should provide the opportunity for all staff to discuss safety issues with management. |
Employee Involvement in Safety Discussions | Safety management methods should serve to provide an opportunity to all staff for open discussion of safety, to identify risks and mitigate against these risks. |
Safety Culture/Climate Monitoring | Management should monitor and review employee thoughts, opinions and feelings concerning the effectiveness of safety management, for example, by conducting safety climate/culture surveys. |
Internal Safety Concern Reporting System | There should be clear and easy to follow procedures to report safety concerns. The reporting system or process should be accessible to all. There should be clear and easy to follow procedures to report safety concerns. The reporting system or process should be accessible to all. |
Approachable Management | There should be opportunities for face-to-face discussion with management, and management should take responsibility for dealing with safety concerns once they have been identified. |
Culture of Trust | Operational staff regularly report concerns when it is appropriate to do so, and reports should be made that concern a range of issues. |
Safety Concern Investigation and Mitigation Procedure | The organisation should take specific steps to monitor known problems, identify new ones, detect trends over time and develop effective preventative measures. |
Safety Concerns Log | All concerns reported should be logged for reference, and efforts should be made by management to analyse repeat or similar concerns. |
Employee Participation in the Change Process | All personnel should be involved in any changes or new initiatives etc. that may affect their job roles. |
Employee Training about the Change | If required, the relevant individuals should be trained to the required level of competence before the change takes place. |
Employee Motivation | Employees should report that they feel involved and included in the change process. |
Active Response to Feedback | There should be strategies in place to communicate the outcomes of the consultation about the proposed change. |
Safety Information Communication System | Safety information (relating to both personal safety and major accident avoidance) should be communicated at the start of the shift or whenever there is a handover of duties. |
Comprehension of Safety Information | Staff should have all the information necessary to conduct their shift safely. |
Employee Awareness of Accountabilities | Personnel should be aware of, understand and adhere to personal accountabilities. |
Safety Prioritised Behaviour | There should be no pressure to maintain performance standards, potentially at the cost of safety. |
Performance vs. Safety Management Priority | There should be evidence that management stipulate clearly and repeatedly to operational staff that safety is the first priority. |
Safety Accountability | Management should take responsibility for the consequences when they prioritise performance over safety. |
Incident Investigation System | Incident investigation procedures should include root cause analysis and ensure that lessons are learnt. Improvement actions should be introduced throughout the organisation. |
Fault Allocation Process | Care should be taken not to apportion blame before the root cause analysis is complete. The purpose of the situation should be to learn from the incident, rather than apportion blame. |
Disciplinary Process | Clear procedures for deciding upon the relevant disciplinary actions should be in place. |
Feedback Systems | There should be strategies in place for communicating the outcome of investigations, eg. via briefings, newsletters etc. |
For further information:
Click here to go to the HSE “Development and validation of the HMRI safety culture inspection toolkit”. HSE RR 365 (2005).